
Food traceability final rule requirements
The FDA is establishing additional traceability record-keeping requirements (beyond what is already required in existing regulations) for persons who manufacture, process, pack, or hold foods the Agency has designated for inclusion on the Food Traceability List. These additional record-keeping requirements are outlined in the “Requirements for Additional Traceability Records for Certain Foods” (Food Traceability) rule and are intended to make it easier to rapidly and effectively track the movement of a food to prevent or mitigate a food-borne illness outbreak.
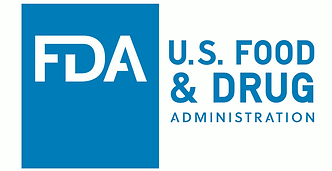
This rule is a key component of the FDA’s New Era of Smarter Food Safety Blueprint and would implement Section 204(d) of the FDA Food Safety Modernization Act (FSMA).
At the core of this rule is a requirement for those who manufacture, process, pack or hold foods on the Food Traceability List (FTL) to establish and maintain records containing Key Data Elements (KDEs) associated with different Critical Tracking Events (CTEs). While the requirements would only apply to those foods on the FTL, they were designed to be suitable for all FDA-regulated food products. FDA would encourage the voluntary adoption of these practices industry-wide.
What are critical tracking events?
Critical Tracking Events (CTEs) are defined as events recorded throughout the supply chain that are essential for achieving food traceability and supply chain visibility. CTEs are dependent on industry standards specific to product categories, growing and processing procedures.
FDA has identified Growing, receiving, transforming, creating, and shipping as Critical Tracking Events (CTEs) for which records would be required.
What are key data elements?
Key Data Elements (KDEs) are the supporting data attributes that define a specific Critical Tracking Event (CTE). i.e. The KDEs required vary depending on the CTE that is being performed.
As per the Food Traceability Final Rule requirement, the records required at each CTE would need to contain and link the traceability lot code of the food to the relevant KDEs.
What's a traceability lot code?
As per the final rule, Traceability lot codes (TLC) are proposed to be a descriptor, often alphanumeric, which is used to identify a traceability lot. The traceability lot code would be established and assigned by:
-
The entity which originates transforms or creates food on the FTL
-
The First Receiver of a food on the FTL and originator did not assign a TLC
New traceability lot codes cannot be established or assigned when other activities in the supply chain are conducted (Example: Shipping, Receiving).
The rule offers flexibility on how TLCs are created:
-
The rule does NOT specify how TLCs should be created
-
The rule does NOT identify any specific KDEs that would have to be included in the TLC
What are the Traceability Data Record-Keeping and Reporting Requirements?
In addition to requiring records of KDEs, the rule would require anyone subject to the rule to establish and maintain traceability program records. These records are intended to help regulators understand an entity’s traceability program.
A description of relevant reference records
A firm’s KDEs might be kept on various types of reference records, such as bills of lading, purchase orders, or production logs. A firm’s traceability program records would need to include a description of the reference records on which the firm maintains the required KDEs. This description would explain where on the reference record the traceability information appears, and if applicable, a description of how reference records for different tracing events for a food are linked.
A list of foods on the FTL that are shipped
The rule would require anyone who ships food on the FTL to keep a list of which listed foods they ship, including the traceability product identifier and traceability product description for each food. This list would be part of a firm’s traceability program records.
A description of how traceability lot codes are assigned
The rule would requires traceability lot codes to be established when a food on the FTL is originated, transformed, or created. The traceability lot code allows a food to be uniquely identified throughout the supply chain. As part of a firm’s traceability program records, firms would be required to describe how they establish and assign traceability lot codes. Because of the crucial role that traceability lot codes play in the final rule, it is important that regulators know how a firm created and assigned these codes so that they can better understand the scope of the records they are reviewing.
Other information needed to understand data provided within the required records
The rule would requires a firm’s traceability program records to include any other information needed to understand the data within their traceability records, such as internal or external coding systems or classification schemes, glossaries, and abbreviations. This will help regulators understand the terminology, methods, and systems a firm uses in its traceability operations.
The final rule requires that:
-
Records are maintained as either original paper records, electronic records, or true copies; they all must be legible and stored to prevent deterioration or loss.
-
Traceability records are provided to FDA as soon as possible but no later than 24 hours after a request is made.
-
An electronic sortable spreadsheet containing relevant traceability information be provided to the FDA within 24 hours of a request when necessary to assist the FDA during an outbreak, recall, or other threat to public health.
Key dates to remember
-
Jan 20th, 2023 - Final rule became law at the completion of 60 days of being published in the Federal Register
-
Jan 20th, 2026 - Companies across the supply chain dealing with items on the Food Traceability List need to comply with the law
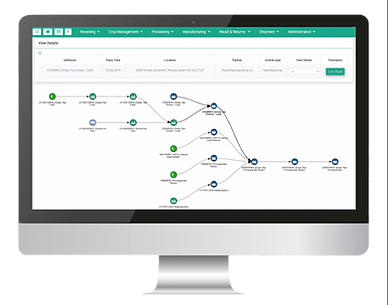
Key points from the final rule
-
Only products on the Food Traceability List (FTL) are in scope.
-
Companies will need to maintain records as original paper records, electronic records, or true copies (must be legible and stored to prevent deterioration or loss).
-
Once requested, companies will need to provide traceability records to the FDA in no later than 24 hours.
-
These records will need to be in an electronic sortable spreadsheet format containing relevant traceability information.
-
Traceability Lot Code - a descriptor, often alphanumeric, which is used to identify a traceability lot.
-
Lot Code Transformation - Lot Code has to be created by specific role based on product (i.e. lot code for a crop would need to come from the Farmer, lot code for processing two products would need to come from the processor).
How to comply with the food traceability final rule
Here are a few steps you can take now to prepare for the Food Traceability Final Rule.
1
2
3
4
Identify products on the Food Traceability List you deal with.
Review what supply chain role you play with each of those products.
Familiarize yourself with the CTEs and KDEs you will be required to track based on your role.
Identify items for which entity has to generate Traceability Lot Code and items for which Traceability Lot Codes should be carried forward.
5
6
7
8
Address any internal process changes to ensure that you are properly aligned with the FDA defined receiving, transformation, creation and shipping CTEs (or growing in the case of farmer).
Drive an internal data readiness progress to ensure these KDE’s are captured and stored in the proper way and are easily accessible.
Talk to your supply chain partners about what they are doing to comply with FSMA Rule 204.
Start vetting different traceability solutions - Traceability projects take time and you should start ASAP.
The TagOne Value

Central Regulatory Repository
TagOne is your Single source of truth for all FDA-related traceability data and documents.

Traceability Data Digitization
TagOne will enable you to Identify, Capture, Validate, Store, and Share relevant traceability data on an “as-needed” basis.

Traceability Reports in Seconds
On a button-click, fetch the TagOne Traceability Map view or Table view report based on Item name/Lot#. This is all you will need in the case of an FDA inquiry.

Traceability Consulting
TagOne is not only your tech traceability platform of choice but our traceability experts will help you navigate this traceability journey every step of the way.